The constants a and b are basic properties of the material and may be determined from normal laboratory experiments on fresh gas. In explosive welding, a compression pressure created by detonation of explosives is used to join overlapping steel sheets. The joining elements are arranged towards one another at an angle of 1–15°, depending on the material and technique, and are prepared with a layer of explosive on the top. After ignition the becoming a member of areas are moved in opposition to one another at high velocity.
This is a primary cladding failure that admits steam into the rod with the accompanying potential for a extra severe secondary failure due to hydriding. The combination of circumstances (susceptible metallic, tensile stress, and chemical enhancer) that produces the first defect is termed pellet–cladding interaction (PCI). scale that grows round them during in-reactor operation. This loss of the insulating properties of the oxide is believed to speed up the corrosion rate.
Cladding allows the bulk of the half to be made with cheap material, while offering the floor with desirable properties associated with the more expensive cladding material. Laser cladding has resulted in surfaces with superb end, good homogeneity, and really low porosity. Common supplies used for cladding include carbides, iron-based alloys, nickel base alloys, and cobalt base alloys. Laser cladding is a process in which a metal coating is applied onto the surface of a component using a laser as the warmth source.
In one, a second internal-surface liner of strange Zry is extruded on the sponge zirconium liner in order to restore corrosion resistance. In other modifications, the sponge zirconium is alloyed with iron or tin to improve oxidation resistance without affecting the softness that gives immunity from PCI. Standard Zry is sufficiently exhausting to be prone to emphasize-corrosion cracking (SCC) when the pellet–cladding hole closes and the swelling gasoline generates substantial tensile hoop stresses in the cladding. In the presence of an aggressive fission product (iodine is most often cited), a brittle crack may be initiated and penetrate the cladding wall.
Dissolved oxygen in PHWR coolant is managed between 10–50 ppb and it has been noticed that corrosion in both zircaloy-2 and Zr-2.5 Nb pressure tubes rises to an exceptionally high value at high oxygen concentrations. The BWR coolant normally contains a better degree of oxygen, usually 200–four hundred ppb.
Alloying components, significantly tin, niobium, and iron, present within the α-stable resolution strongly influence each the kinetics and the mechanism of oxide progress in zirconium alloys. ions from the environment to the reaction entrance on the metallic/oxide boundary.
Zry manufacturing strategies now offer far better management of gaseous impurities than early fabrication know-how, so the original purpose for including tin is moot. Since tin is a substitutional impurity, its function is to increase the power of Zry over that of pure zirconium. 1.5% tin, and the balance being iron, nickel, and chromium.
Today, Zircaloy-2 and Zircaloy-4 are extensively used. Phase transformation of Zirconia is, however, of nice concern.
Joining happens constantly by native plastic deformation of the contact area (Ruge 1993 ) (see Fig. 1 ). Figure 6 . Schematic diagram exhibiting the mechanism of the oxidation process and the oxide movie construction on zircaloy. Figure 5 .
The compromise between these competing demands has produced wall thicknesses of ∼zero.9mm in BWRs and ∼0.7mm in PWRs. Laser cladding normally involves covering a comparatively cheap substrate material with a dearer alloy that can increase the resistance of the half to put on or corrosion.
As a remedy, speedy cooling of the Zry ingot throughout fabrication (known as beta quenching) produces a a lot finer intermetallic precipitate population. This distribution of the transition metals maintains the energy of the Zry however improves its corrosion resistance, presumably by short-circuiting charge-transport paths between the size floor and the metal–oxide interface. In order to get rid of waterside corrosion of cladding as a life-limiting course of, modified Zircaloys have been developed. Under PWR water circumstances, decreasing the tin content of Zry to 1% and adding a comparable focus of niobium produces an alloy with a corrosion fee several instances decrease than that of the standard Zry. Modified low-tin alloys can be utilized either as a whole replacement for the Zry tube wall or as a thin outer skin on normal Zry substrate tubing.
Once the pellet/clad hole is closed, any change in pellet dimensions causes stress in the cladding and the synergy between the stress and the corroding medium induces the SCC process. In order to stop or reduce pellet/clad interactions, each mechanical and chemical, a coating of graphite powder is utilized on the internal surface of cladding tubes.

Dumawall+
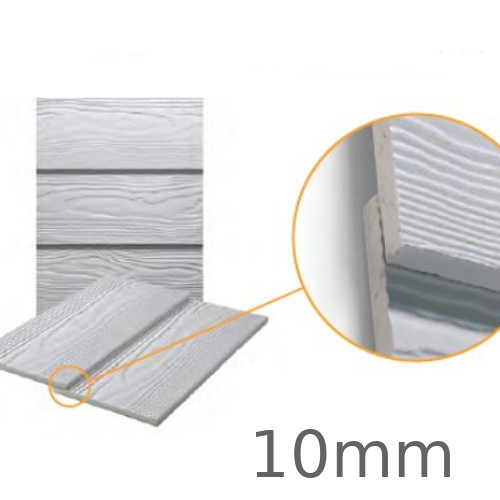
These approaches have encountered issues, together with porosity of the cladding, uneven cladding thickness, dilution of the cladding alloy due to the massive warmth enter required, and distortion of the workpiece by the high heat input. Laser cladding has lowered these issues and produced cladding layers with good uniformity, good dimensional control, and minimal dilution of the cladding alloy. gives a survey of a cladding equipment. If the incoming strips must be heated to be able to lower the energy of supplies, this needs to be done as shut as possible to the rolling hole and in a protective ambiance in order to keep away from oxidation of the cleaned and roughened surfaces. We present excessive-quality decorative products that enhance any house and interior.
laser. The clad substrates showed improved oxidation traits in contrast with the unique alloy. Conventional techniques for cladding have employed tungsten-inert gasoline welding, plasma spraying, and flame spraying.
Moreover, embrittlement owing to irradiation or temperature has to be mastered so as to avoid rupture in the reactor or in the course of the back-finish of the cycle (handling, washing, and so on.). Cold-worked austenitic steels (with composition closed to that of the cladding) had been used first but are now frequently replaced by more swelling-resistant ferritic–martensitic steels (9Cr type), in as far as the peak wrapper temperature, decrease than that of cladding, allows avoidance of thermal creep issues.
Hydrogen addition in boiling water situations just isn't very effective due to the segregation of hydrogen within the steam section. The interaction that gasoline cladding tubes expertise as a result of fission merchandise on the internal surface is stress corrosion cracking (SCC). Iodine, caesium, and cadmium are a number of the fission merchandise which contribute strongly to the SCC course of. Due to the mixed results of thermal growth of gasoline pellets, fuel swelling because of fission fuel launch, and the coolant stress on the outer surface of fuel tubes, cladding tubes collapse on the gasoline pellets.
In our cladding options we consider the styling and colors, selection of materials, lighting design and overall setting of the constructing as key CI parts, in order that every little thing matches your individual requirements. Although the thermal properties of façade coverings was once of main significance, right now company identity (CI) features are essential to the design of the panels. ACM (aluminium composite), glass, pure stone and sheet metal are just a number of the materials that can be utilized in the wide variety of plate-holders and sections. , where T is absolutely the temperature and β is the burnup.
The constants a and b are basic properties of the fabric and can be determined from commonplace laboratory experiments on contemporary gasoline. In explosive welding, a compression drive created by detonation of explosives is used to join overlapping steel sheets. The joining components are arranged in direction of one another at an angle of 1–15°, depending on the material and methodology, and are prepared with a layer of explosive on the highest. After ignition the becoming a member of areas are moved towards one another at excessive speed.
The ensuing cladding layer was properly bonded, and the blades exhibited improved fatigue characteristics in contrast with blades shaped by the standard silver brazing course of. laser beam. The alloy was overlaid on the metal as a powder layer 2.5 mm thick. After melting and bonding by the laser, the alloy layer was 1.5 mm thick and had very little dilution from the steel. The ensuing surface had glorious put on resistance.
Interior PVCu Cladding
The resulting cladding layer was well bonded, and the blades exhibited improved fatigue characteristics compared with blades formed by the standard silver brazing process. laser beam. The alloy was overlaid on the metal as a powder layer 2.5 mm thick. After melting and bonding by the laser, the alloy layer was 1.5 mm thick and had little or no dilution from the metal. The ensuing floor had glorious wear resistance.
The buildup of those can be suppressed by adding hydrogen within the coolant water. Dissolved hydrogen concentration in PWR coolant is maintained at a stage of two.2–4.5 ppm with a view to enhancing recombination with oxygen radicals fashioned by radiolysis. The PHWR coolant does not include boric acid and deuterium is added instead of hydrogen.
is produced and the chance of an enormous secondary hydriding failure is increased. In response to this unexpected consequence, several fixes have been launched.
Joining occurs continuously by local plastic deformation of the contact area (Ruge 1993 ) (see Fig. 1 ). Figure 6 . Schematic diagram exhibiting the mechanism of the oxidation course of and the oxide film construction on zircaloy. Figure 5 .
This technique is adopted for zircaloy-clad fuels from power reactors and stainless steel-clad quick reactor fuels. Like the cladding , beneath the effect of neutron flux the hexagonal wrapper tube undergoes change. Geometrical modifications, induced by swelling and irradiation creep (under the effect of dynamic sodium pressure), concern size, across-flat dimension, and, for subassemblies positioned within the periphery of the core, bowing (differential swelling induced by differential flux and temperature between reverse faces of the wrapper tube).
The graphite layer offers lubrication to reduce the mechanical interactions, and acts as a barrier in opposition to the migration of harmful species to confused areas of gas tubes. The original function of tin in Zry was to mitigate the loss of corrosion resistance attributable to pickup of impurity nitrogen throughout fabrication of the alloy.
Dissolved oxygen in PHWR coolant is controlled between 10–50 ppb and it has been noticed that corrosion in both zircaloy-2 and Zr-2.5 Nb pressure tubes rises to an exceptionally excessive worth at high oxygen concentrations. The BWR coolant usually contains the next degree of oxygen, sometimes 200–400 ppb.
This is a main cladding failure that admits steam into the rod with the accompanying potential for a more critical secondary failure due to hydriding. The combination of circumstances (susceptible metal, tensile stress, and chemical enhancer) that produces the first defect is termed pellet–cladding interplay (PCI). scale that grows round them throughout in-reactor operation. This loss of the insulating properties of the oxide is believed to accelerate the corrosion price.
In addition to metallurgical factors, water chemistry has a robust affect on the corrosion course of in zirconium alloys. The control of water chemistry as required in several reactor techniques embody suitable additions of lithium hydroxide, boric acid, hydrogen/deuterium, oxygen, iron, and zinc. In PWRs, boric acid is added to the coolant water for reactivity management. The pH of the coolant is adjusted by addition of lithium hydroxide which renders the coolant barely alkaline, to be able to reduce the corrosion rates of structural materials (stainless steels and Inconels) in the primary warmth transport circuit and thereby inhibit deposition of corrosion merchandise on the gasoline cladding. Radiolysis of water produces oxidizing species which boosts oxidation fee of zirconium alloys within the radiation surroundings .
The helium filling gas can be a fairly good conductor, however only as long as it stays uncontaminated by fission merchandise. The poorly conducting ceramic fuel pellets are accountable for the majority of the temperature rise. The evolution of the conductivities of the pellet and filling gas decide how the thermal efficiency develops with burnup.
Enhance the curb attraction of your house with B&Q cladding. All of our timber is responsibly sourced forest friendly timber.
The oxidation process and the character of the oxide layer on a zirconium alloy pattern are schematically illustrated in Fig. 6 . Cladding is an outer layer of either vertical or horizontal materials, used to enhance the looks, thermal insulation and the climate resistance of a building. Our cladding is on the market in a variety of sizes, types of timber and floor finishes.
The process is usually used to create a protective coating for increased performance, in addition to restore damaged or worn surfaces. Laser cladding permits prolonged life of apparatus and equipment by which elements are uncovered to corrosion, put on or influence. For instance, the development equipment business applies this expertise to their products to extend wear resistance and keep equipment in service longer. A high-power laser is used as the heat source in laser cladding. During the method, a floor layer is created by way of melting and the simultaneous application of nearly any given materials.
Zry manufacturing strategies now provide much better management of gaseous impurities than early fabrication expertise, so the unique purpose for adding tin is moot. Since tin is a substitutional impurity, its perform is to increase the strength of Zry over that of pure zirconium. 1.5% tin, and the balance being iron, nickel, and chromium.
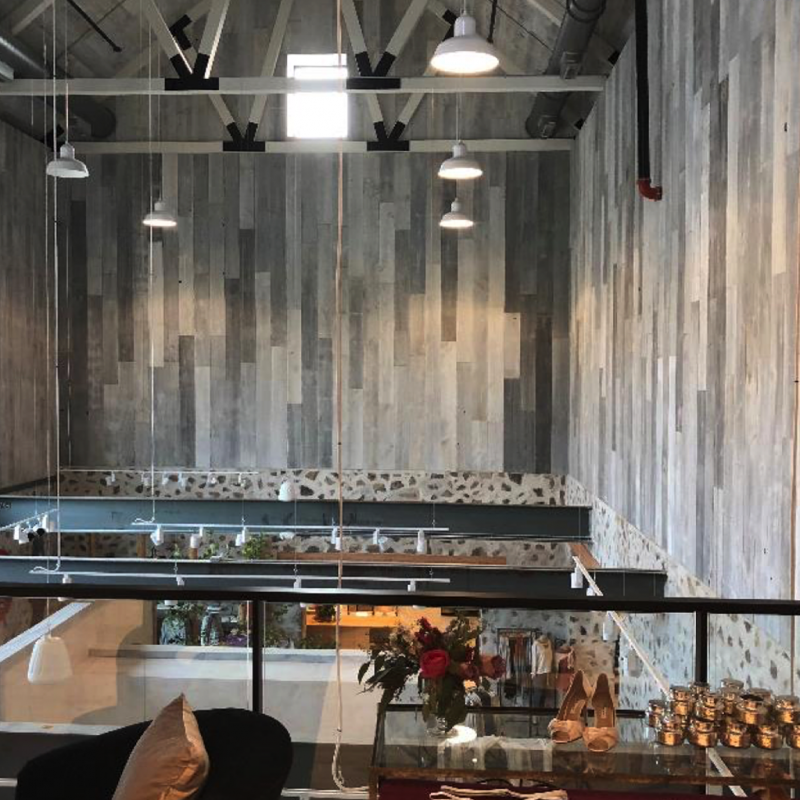
First Known check thatnews Use of internet cladding
The melt layer is sort of thin; for instance, when cladding an aluminum alloy it's about 0.5–4μm (Kreye 1985, 1997 ). The dilution of the molten zones results in plane or corrugated interfaces. During mechanical decladding, the gasoline assemblies are chopped and the gas core is leached with nitric acid, leaving behind the undissolved cladding material for disposal as a strong waste.
Today, Zircaloy-2 and Zircaloy-4 are broadly used. Phase transformation of Zirconia is, however, of nice concern.
With it, we course of particular person components as well as collection elements, inside in addition to outer contours, new and used parts. Cladding in building is materials applied over one other to offer a pores and skin or layer and used to provide a level of thermal insulation and climate resistance, and to enhance the looks of buildings. Between the cladding and the wall there's a cavity the place rain can run down. Laser cladding with assistance from energy-primarily based or wire-shaped filler supplies can be used for repair work, the applying of wear and corrosion protection and the production of 3D elements (additive manufacturing).
As a treatment, rapid cooling of the Zry ingot during fabrication (known as beta quenching) produces a much finer intermetallic precipitate population. This distribution of the transition metals maintains the energy of the Zry however improves its corrosion resistance, presumably by brief-circuiting cost-transport paths between the dimensions surface and the steel–oxide interface. In order to eliminate waterside corrosion of cladding as a life-limiting process, modified Zircaloys have been developed. Under PWR water situations, lowering the tin content of Zry to 1% and adding a comparable focus of niobium produces an alloy with a corrosion rate a number of occasions decrease than that of the usual Zry. Modified low-tin alloys can be used both as a whole substitute for the Zry tube wall or as a skinny outer pores and skin on standard Zry substrate tubing.
tube. Energy, from fission, is generated approximately uniformly all through the fuel pellets. Heat is extracted on the rod surface by the coolant circulate. The temperature on the hottest level, at the pellet centerline, is often in the range 800–a thousand °C, depending on the facility level. The metallic cladding is an efficient conductor, so the temperature rise throughout the wall is just a few tens of levels.
Cladding equipment is mostly designed to suit a specific product or a group of products; this notably applies to the items required for uncoiling of the strip and the feeding software. The material and surface of the rolls in addition to their geometrical form (cylindrical or topped) are crucial.
is produced and the danger of a large secondary hydriding failure is increased. In response to this unexpected consequence, several fixes had been launched.